C2 PROJECT
C2 Project News
July 2025
News from the July 2025 working party
The challenges of working to high precision
The working party started with Dave 1 carrying out some preparatory work. Firstly, he found the container of pins and links which will be needed to reassemble the draincock operating mechanism. We previously removed this, as it was in the way while assembling other parts, but we want to have the linkages in place before finalising the design of the reverser reach rod.
The front section of the reverser reach rod lies below the draincock reach rod, and has to include a lateral wiggle to connect the regauged reverser weighshaft cranks and the screw reverser in its original position in the cab. It looks fairly straightforward, but careful checking is still worthwhile.
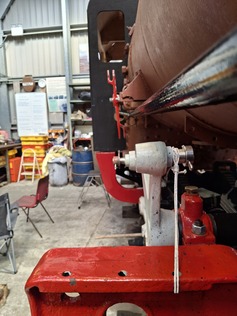
View showing the misalignment between the reverser weigh-shaft crank and and the intermediate crank bolted to the side of the boiler. The misalignment is due to the regauging from 762mm gauge to 597mm gauge.
Next on Dave's job list was to mark, drill and tap holes in the crosshead lower slippers, to allow them to be held in place while machining them in situ. The original holes in the crosshead were 10.5mm diameter, but are badly worn, so we will therefore ultimately drill them out to 12.5mm. Drilling the slippers at 8.5mm diameter and then tapping them to M10 will allow us to fit temporary screws into them from below, using the existing holes in the crossheads. Since this presents a risk of machining the ends of the screws, we bought brass M10 screws to avoid the machining operation encountering sudden changes in hardness of material.
New cross head slipper drilled and tapped.
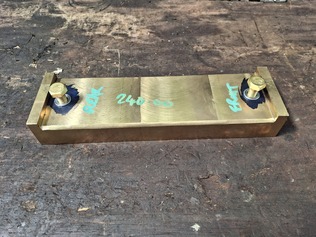
You may recall that the plan was to put the piston rods (with pistons still on the ends) into the crossheads, then use the piston rod as a datum when machining the slippers. To this end, Dave 1 screwed the Fireman's side crosshead lower slipper into place, and he and Andrew moved the crosshead, dummy little end bearing pin (with end extensions), and the corresponding piston and rod into the machine shop.
The components were assembled on the milling machine. The piston rod was placed in a matching pair of V-blocks, and the dummy little end bearing pin was placed in two more. Some careful packing and shimming was necessary to get the pairs of V-blocks at the correct height relative to each other.
With the piston rod in its pair of V-blocks, it seemed fair to assume that it was horizontal on the bed of the milling machine. This then made it possible to run a dial test indicator along the side of the piston rod to get it parallel with the longitudinal axis of the machine.
After some tweaking we were happy that the piston rod was aligned. But we thought it might be worth checking that the piston rod was perfectly horizontal. A run up and down with the dial test indicator showed a 12 thou misalignment over 500mm. Never assume that the V-blocks are perfectly matched! So we repacked all the V-blocks to compensate for the 12 thou error we'd found, and then rechecked the lateral alignment (clocking against a round surface relies on at least one axis being perfectly aligned, otherwise you get false readings).
All this takes a considerable amount of time, and we spend much of one day checking that the piston rod was perfectly aligned with the table of the milling machine. Repeat measurements with the dial test indicator in both vertical and lateral planes eventually showed that we'd got there.
Next, we had to line up the milling cutter over the centre of the piston rod. Erle came to the rescue with an edge finding gadget. Placed against one side of the piston rod and then the other, two lateral readings were obtained on the digital read-out of the milling machine. Moving the tool to the average value of the two readings places it directly over the centreline of the rod.
By the end of the day we were ready to take a first cut. Dave had found a 2 inch diameter carbide tipped milling cutter which he'd used before, and which might just be long enough to reach down between the sides of the crosshead to make a full depth cut. The slots for the slidebars are 56-57mm wide, so the 2 inch cutter should take out most of the material which needed to be removed before we finish off the edges of the slot.
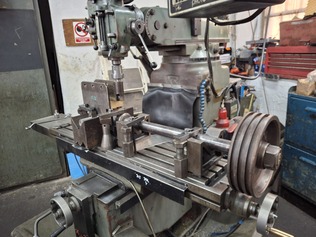
Milling machine set up to machine the cross head slippers parallel to the piston rod and perpendicular to the little end bearing pin.
Brass is an easy cutting material, so we started with a 2mm deep cut. The cutter didn't sound entirely happy, although adjusting the speed did seem to improve things somewhat. At that point we decided to leave the job until the following morning when the Works' staff would be available to give us advice.
Taking a second 2mm cut the following morning soon attracted attention. Dewi suggested an end mill might be a better tool, while Merik noted that the chattering was likely due to cutting on both sides of the slot simultaneously, which also resulted in a less than perfect finish on the sides. Dave thought this odd, since he had used the same cutter in the same way before, but on the much chunkier Bridgeport milling machine (unfortunately currently out of action), without such problems.
The slot in the slipper needs to be about 14mm deep, so we have plenty of material to play with. By now we had a 4mm deep slot, which is deep enough to be able to measure the sides. Andrew and Dave began to wonder if taking the slipper out of the crosshead and mounting it directly on the bed of a milling machine (and potentially using a shorter cutter) might avoid the chatter. We could use the existing part formed slot as a datum to set it up with, knowing that it should now be perfectly aligned with the piston rod.
The width of the slot is easy to find, as we know the centre of the part-formed slot is also the centre of the finished slot. But we didn't know exactly how much more material would need to be removed from the bottom of the slot. To find this, we placed a parallel on the bottom of the slot and took measurement to the piston rod.
View down the length of the piston to the cross head slipper.
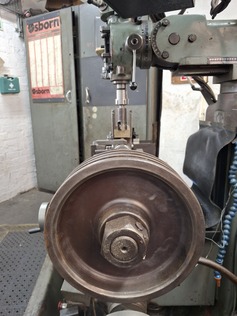
At this point things got very confusing! The measurements showed that the parallel (and hence the bottom of the slot) was not parallel to the piston rod. Could something have moved? We set up the dial test indicator again and remeasured the piston rod. No; it was still perfectly level. So perhaps the slipper had moved. We used the dial test indicator to measure the bottom of the slot. It was also, as close as we could measure, perfectly level. This tells us that we have two parallel surfaces with an angle between them; a real contradiction!
Keith had the misfortune to be walking past as Andrew and Dave scratched their heads, and got collared. The problem was explained and Keith gave it some thought. After looking over the set-up on the milling machine, with the workpiece at one end of the table and the piston overhanging the other (both heavy components), he suggested that perhaps there was sufficient flex in the machine itself to result in measurements at opposite ends to be out of true.
While it was annoying that we we not going to be able to machine the slippers in situ, as originally planned, all was not lost. We had already started to think about taking the slipper out before final machining, and the problem with the milling machine flexing just gave extra weight to that argument. Even though the bottom of the slot is not parallel to the piston rod, we can measure how out of true it is, and then shim the slipper before machining it to correct the error.
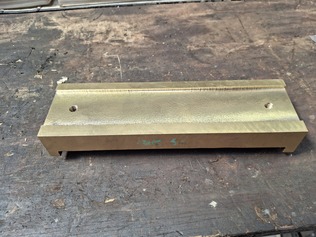
New cross head slipper following initial machining.
At this point we were at lunch time on the final day of the working party, so we decided not to start setting up the slipper for machining separately. That can take place at the next working party. So all the components were disassembled and returned to the C2 Shed, and all the equipment used returned to its correct home. We've learned a lot about the limitations of machines, so we hope that the next stages will be somewhat quicker and will give us the precision we wish for.
Erle joined us for a couple of days, and continued to work on the reverser operating handle. He has now formed the crank which holds the handle. Being made of stainless steel it is not easy to machine, with the countersunk holes for attaching the crank to the indexing wheel being particularly challenging. But, as is usual with Erle's work, the results are amazing!
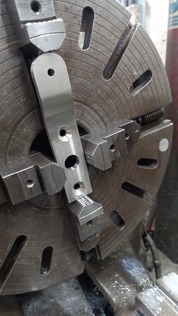
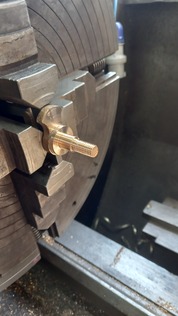
Erle machining the new screw reverser handle in a 4 jaw chuck.
The new reverse handle made by Erle beside the old components.
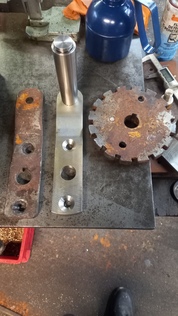
Erle has also been busy making window frames for the NG15. Again, they are absolutely beautiful! The traditional brass window frames of the NG15 make an interesting contrast with the purely functional rubber window seals of the C2. Deciding which is the better design is likely to depend on whether you are admiring the locomotive or polishing the brass!
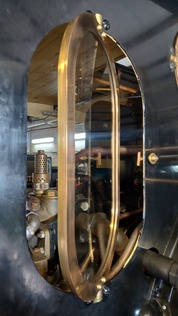
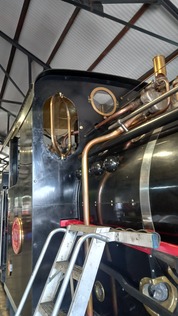
NG15 cab window fitted.
Dave 2 managed to spend an hour with us on the final afternoon. We couldn't let him get away with just a social visit, so he was given the M20 castle nuts we recently purchased, and was asked to fit them to the front ends of the slidebars. It didn't take Dave long to replace the existing standard nuts with the castle nuts, and to drill holes for split pins in the outer studs. The inner studs are more challenging, as it isn't possible to get the cordless electric drill in. Dave thinks he has a flexible drive for an electric drill at home, which will hopefully make it possible to drill the inner studs.
With work on the crosshead slippers on pause until the next working party, Andrew and Dave 1 spent the final afternoon on some admin type tasks. Andrew has measured and drawn the existing (Chinese designed) tender axle end covers and bearing retainers, so he and Dave checked and finalised the drawings of them. The interfaces with the axle end and axlebox will be used in the design of an axle end adapter to mount the speedometer generator.
Sam has offered to make contact with boiler manufacturers in order to get quotes for the new boiler. He, Andrew and Dave 1 therefore had a telephone conference to try and progress that task.
As usual, spending an hour at the end of the working party tidying the C2 Shed is highly beneficial. It makes the next working party so much easier if everything is in its correct home and you can actually see the workbench!
In summary, we knew that machining the crosshead slippers was going to be a challenge, but we are not disappointed that we didn't complete the task. We have learned what we need to do, so finishing the Fireman's side looks possible at the next working party, and we'll then have a proven method we can use for the Driver's side which will hopefully be much quicker.